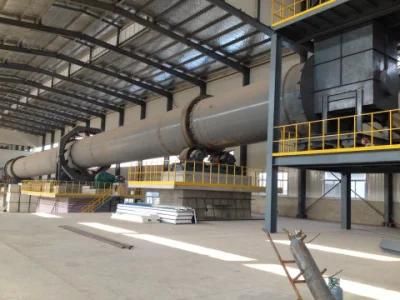
Cement Rotary Kiln Support Roller
Luoyang Zhongtai Industries Co., Ltd.- After-sales Service:24 Hours on Line
- Warranty:One Year
- Weight:From 3 Tons to 200 Tons Per Piece
- Standards:ASTM,BS,NF,DIN,JIS and So on;
- Certificate:ISO 9001:2008
- Transport Package:Standard
Base Info
- Model NO.:Cement Rotary Kiln Support Roller
- Specification:Rotary kiln support roller
- Trademark:LYZT
- Origin:Luoyang, Henan
- Production Capacity:2000PCS,Year
Description
Basic Info.
Model NO. Cement Rotary Kiln Support Roller Specification Rotary kiln support roller Trademark LYZT Origin Luoyang, Henan Production Capacity 2000PCS/YearProduct Description
Product Description
Rotary Kiln Support Roller
Kiln Support Rollers are backed by latest technology and provide desired support to cables and other related products. These support rollers are driven to rotate using friction between roller surface and web. The small friction torque of the roller bearings also allow higher speed operations and helps in avoiding possibilities of slippage due to presence of large air film between roller surface and web.
Features :
Coming with small friction torque of roller bearings
Rollers are close together that decrease pulling tension
Manufactured as per defined industry standards
Can also be custom designed as per client's specific requirements
Durable finish and reliable performance
Rotary Kiln supporting roller:Cemen Rotary Kiln supporting roller and Lime Rotary Kiln supporting roller
We bring forth to our customers Kiln Support Roller for a Rotary Kiln that are designed by our experienced processionals, who hold vast knowledge in this domain. Our professionals uses refractory material that are lined to protect the steel shell and reduce radiation losses.
Rotary Kiln Supporting Roller Assembly |
We are manufacturer and reputed suppliers for the Kiln Support Rollers Assembly for various plants as mentioned below:
Sponge iron plants
50tpd, 100tpd, 200tpd, 300tpd, 350tpd, 500tpd plants for various design consultants in markets, like:
od1700mm x id550 x 880mm
od1800mm x id500 x 1000mm
od1000mm x id320/300 x 560/550mm
od400mm x id160 x 240mm or any customized design.
Cements plants for any capacities
Alumina plants
Phoshphate mines
Kaolin & bentonite plants
Weight: from 3 tons to 200 tons per piece
The supporting roller is the necessary part of the rotary kiln.
We are professional in manufacturing the fittings for large mining machinery. Our supporting tyre and roller is mainly used on large rotary kiln.
Our casting steel piece is mostly lighter than 200 tons. After the ultrasonic flaw detection, our product reaches the second level of the GB standard.
Material:Carbon steel,low alloy steel:ZG20SiMn,ZG50Mn,ZG35SiMn,ZG35CrMo,ZG35SiMnMo,
ZG42CrMo,ZG40Cr,ZG34CrNiMo,ZG40Mn and so on.
Process:Place a pattern in sand to create a mold;
Incorporate a gating system;
Remove the pattern;Fill the mold cavity with molten metal;
Allow the metal to cool;
Break away the sand mold and remove the casting.
Heat treatment.
Chemical composition test,UT/MT test,mechanical property test and so on.
Surface treatment and other requirement from customer.
Standard&certificate:ASTM,BS,NF,DIN,JIS and so on;
ISO 9001:2000;BV,CCS,DNV,NK,RINA,KR and so on.
Weight:from 3 tons to 200 tons per piece
Application:
The products can be widely used in the area of cement mill,rotary kiln,shipbuilding,
metallurgy,mine,sugar mill,powder plant,rail road,engine bed and so on.
We can provide OEM service for cement mill and rotary kiln casting parts,marine steel casting parts,sugar mill machinery parts with carbon steel or low alloy steel.
The casting parts can be supplied as following treatment:
Heat Treatment: Normalized, normalized and tempered,quench and tempered
Machining: Rough machined,semi-finished machined,finished machined
Quality warranty and testing equipment:
Magnetic powder inspection
UT nondestructive test
Dye inspection
Leeb hardness testing equipment
Mechanical property test equipment
Metallographic microscope
Direct-reading spectrometer
Features of our products:
Durable
Excellent tensile strength
Accurate level of tolerance
Good dimensional accuracy
Superb surface finishing
Easy to use and install
Possible defects:
Defect | Causes |
Unfilled sections | Insufficient material Low pouring temperature |
Porosity | Melt temperature is too high Non-uniform cooling rate Sand has low permeability |
Hot tearing | Non-uniform cooling rate |
Surface projections | Erosion of sand mold interior A crack in the sand mold Mold halves shift |
There are no these problems for us.
Uniform wall thickness will ensure uniform cooling and reduce defects.
A thick section, often referred to as a hot spot, causes uneven cooling and can result in shrinkage, porosity, or cracking.
Corners
Round corners to reduce stress concentrations and fracture
Inner radius should be at least the thickness of the walls
Machining allowance
Add 0.0625 - 0.25 in. (0.16 - 0.64 mm) to part dimensions to allow for machining to obtain a smooth surface.
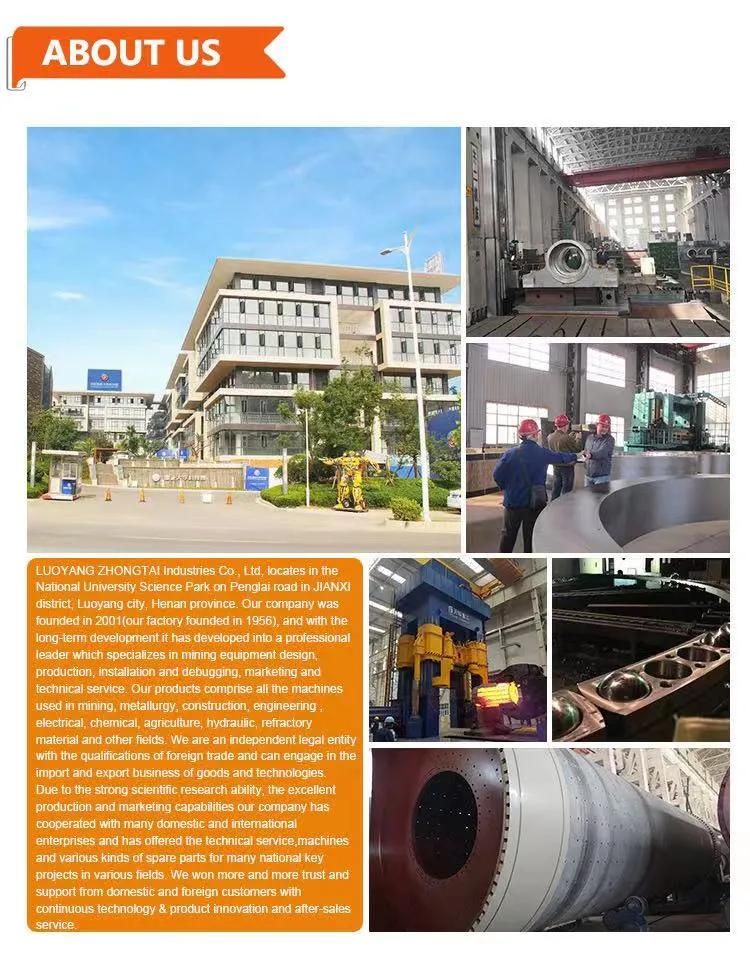
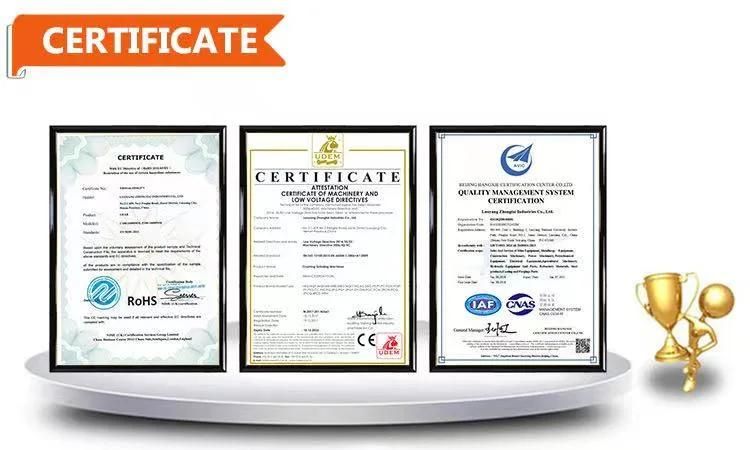
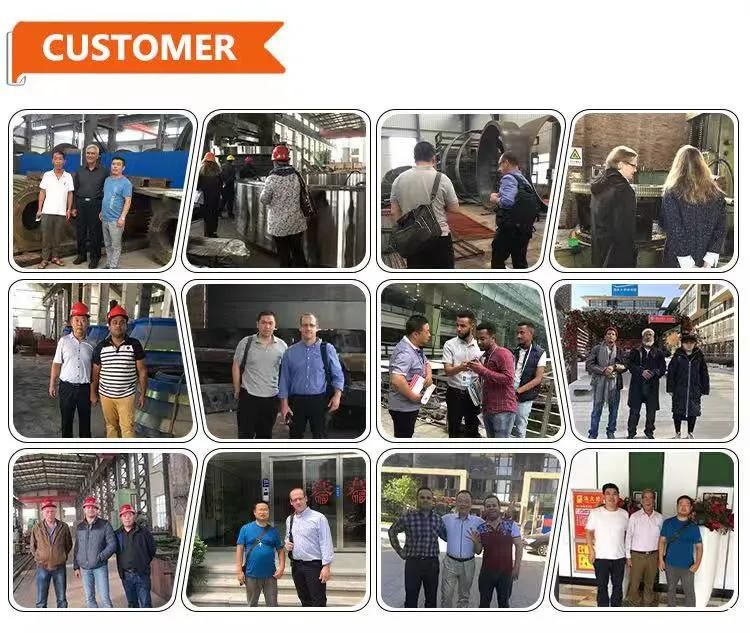
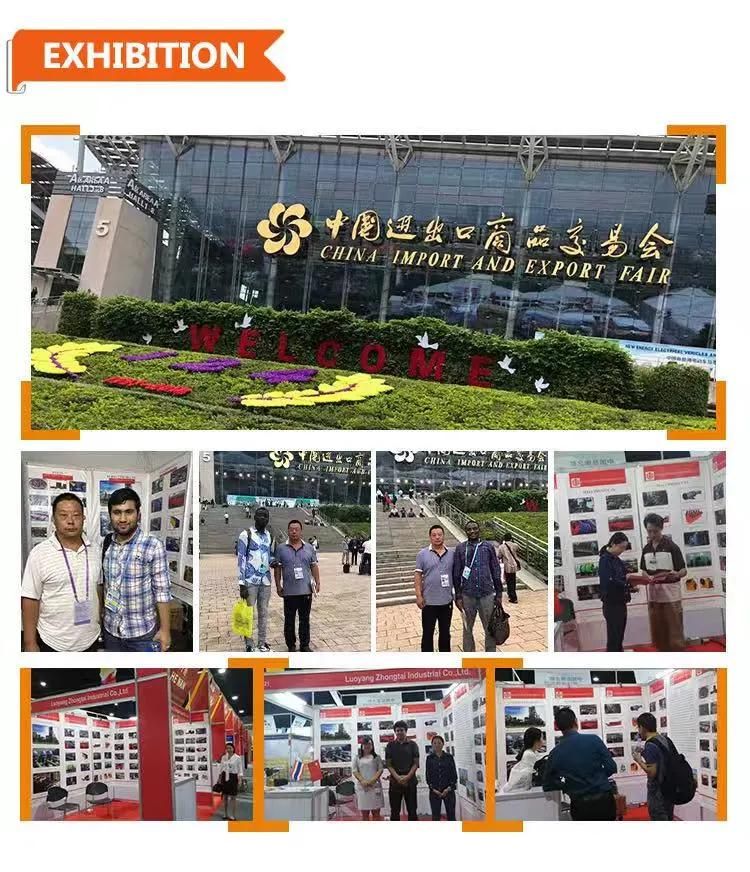