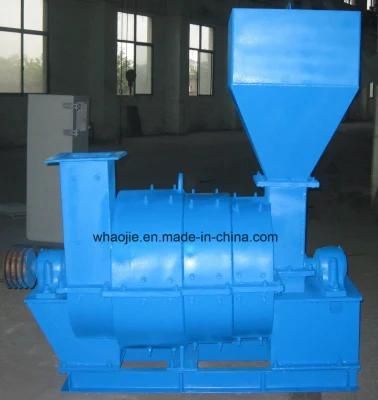
Energy-Effcient Horizontal Coal Grinding Machine
Wuhan Aojie Technology Corporation- Type:Ball Mill
- Application:Chemistry
- Materials:Coal
- Condition:New
- Capacity(Kg/H):500
- Outlet Temperature:350-1400
Base Info
- Flame Length:1.5-3
- Motor(Kw:15
- Revolution r.p.m:2400
- Pulverizer Model:High-Speed Hammer Type
- Transport Package:Standard Export Package
- Specification:WHAJ-M -500
- Trademark:WHAJ
- Origin:Wuhan
- Production Capacity:500000PCS
Description
Model
WHAJ-M -150
WHAJ-M-300
WHAJ-M -500
WHAJ-M -600
Capacity(kg/h)
150
300
500
600
Outlet temperatureºC
350-1400
350-1400
350-1400
350-1400
Flame length
1.5-3
1.5-3
1.5-3
1.5-3
Pulverizer Model
High-speed hammer type
High-speed hammer type
High-speed hammer type
High-speed hammer type
Motor(KW)
7.5
11
15
18
Revolution r.p.m
2600
2200
2400
2400
2. Structure and working principle
2.1 Structure
2.1.1 Pulverizer composition
It is composed by coal bucket, shells, spindle, hit coal Hammer, linings, fan, separator, equipped with bearing chamber, cylindrical roller bearings in the shell at both ends, sealing bearing chamber and bearing with felt circle, adding seal ring in latter bearing ring, fixing bearing chambered at both ends of the body with caps sealed.
2.1.2 Pulverizer
Composed by crushing chamber and fan room, 2 sets of devices are equipped on the rotating shaft, drove by Y series motor and V-belt. Machine body is composed by upper and lower shell. There is coal feeding inlet and air inlet in the upper shell with baffle adjusting the amount of wind. Pulverized coal and air are mixed in the upper part of the fan room. Foot of lower shell and channel steel are fixed with bolt. Fixed liner and side panels are fixed inside the crushing chamber. Fixed fan is installed on the shaft in the fan room.
2.1.3 pulverized coal and separator
The bottom separator is connected with upper shell; pulverized coal pipe is connected with rubber pipe on the top; connection of return pipe for large-sized pulverized coal particle and feeding inlet are welded on the top diagonal plane of separator.
Pulverized coal can be combusted completely and provide high heating intensity for dryer to improve the dryer heating intensity, decrease heating loss and stabilize the temperature.
2.1.4Working theory
Coal feeding, coal injection, coal pulverizing, coal separation process are completed on the main machine. Adjusting of the flame temperature is achieved by controlling coal feeder through the electric vibrator. Pulverized coal less than 0.1mm will be separated and then fanned to be combusted. For those larger then 0.1mm, it will fall down into the bottom of the separator and be reground in the crushing chamber through return pipe.
Return pipe of the separator need to be checked constantly to prevent clogging. By using pulverized blowing technology and maximizing contact area of the coal and oxygen, our machine has very high burn-off rate. Moreover, fast operation and rotation of the pulverized coal speeds up the carbon combustion rate.
Speeding coal combustion and flame rotation, along with semi-enclosed combustion chamber and reasonable air supply, it not only helps efficient combustion, but also greatly reduces the heat loss.
The pulverized coal in the combustion chamber is almost burning fiercely and immediately, providing heat instantly to the dryer. Except some heat is absorbed by refractory in combustion chamber, most of its heat is sent into the dryer.
2.1.5 Process flow for raw coal combustion and the heat outputting:
Raw coal --- crushing chamber --- inhaled by fan machine and discharged --- pulverized coal separation --- rotated by the pulverized coal pipe --- ignition --- rotating suspension burning - - flame injecting --- to heat needed equipment
3. Equipment installation and operation
3.1 Equipment assembly
Main machine should be installed on a concrete foundation and adjusted to be horizontal, fixed with anchor bolt. With Rubber pipe, pulverized coal separator is connected to the furnace and adjusted the mounting height. The furnace base should be smooth, fixed with brick concrete structure or steel base. Main machine connects wind exhaust pipe in fan and wind pipes in burner ignition chamber. The connection of the ignition furnace and combustion chamber will be brought into fire hole, 150-200mm. the combustion chamber required to be connected with heat source device.
3.2 Operation
L <20mm raw coal is loaded in the bucket of the storage, requirements for coal:
- Calorific value: 4500-6000 kcal / kg, generally 5000 kcal / kg; volatile V ≥ 25%.
- Long-flame coal or non-caking coal will be the best choice, plastic layer Y should be less than 10mm.
3. Moisture: 3-5%. It can only be used after drying if mixed with rain, snow.
4. Ignition
Wood is ignited in the ignition furnace with the help of the air fan. It takes about 30-40 minutes to reach 700 ºC -800 ºC in the furnace for the first time. Then the coal pulverizer can be started off.
3.4 Note:
Pay attention to the electrical instrument and observe the equipment operating conditions. Once exception happens, it needs to stop and check immediately, checking various bolts, bearing. After continuous operation for 24 hours, bearing chamber should be injected lithium based grease oil. The normal operation can be ensured only after the return pipe is unobstructed.
4.Equipment repair and maintenance
4.1 Equipment Maintenance
After the shutdown, bolts in each part needs tobe checked to ensure it is notloose.Amount of lubricating oilbefore and afterthebearing chamberneeded to be checked and rechargedin time.
4.2 Equipment Maintenance
Maintenance of equipment todo the following:
Bearing lubrication statusofbearing chamberneed to be checked, cleaned and replaced with newgreaseif grease fouling.
Check the external bolts and sturdy.
Open the main machine and check coal hammer working condition. If worn out, it needs to be replaced with new parts.
Check whether liners and bolts in the crushed parts are loose. If broken seriously, it needs to be replaced with new parts.
Check whether connecting bolts in fan blades are loose. If the blade is badly worn, it needed to be replaced with new parts.
Check the combustion chamber, clean fouling and repair the lining.