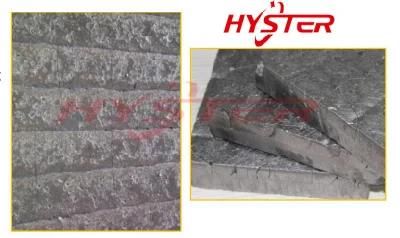
Chromium Carbide Overlay Plate Compound Plates Wear Resistant Plates
Hunan Hyster Material Technology Co., Ltd.- Certification:ISO 9001:2008
- Standard:ASTM
- Surface Treatment:Polishing
- Manufacturing Process:Casting
- Material:Cast Steel
- Name:Chromium Carbide Overlay Plate
Base Info
- Model NO.:1500x3000 , 1200x2400
- Hardness:Around Hv600
- Cutting:Plasma,Laser Cutting,Water Jet Knife
- Cold Forming:Min. Radius 150mm(6+4)
- Transport Package:Polywood Crates, Pallets, Oil Film
- Specification:High Grade
- Trademark:HYSTER, OEM, DUAPLATE, DOMITE
- Origin:China Hunan
- HS Code:7225990
- Production Capacity:200 Ton,Month
Description
Basic Info.
Model NO. 1500x3000 / 1200x2400 Hardness Around Hv600 Cutting Plasma/Laser Cutting/Water Jet Knife Cold Forming Min. Radius 150mm(6+4) Transport Package Polywood Crates, Pallets, Oil Film Specification High Grade Trademark HYSTER, OEM, DUAPLATE, DOMITE Origin China Hunan HS Code 7225990 Production Capacity 200 Ton/MonthProduct Description
Chromium Carbide Overlay PlateDescription
The refined microstructure within the Hyper wear plate overlay is based on a "micro-carbide" system, which combines the improved wear resistance and impact resistance of the martensitic and chromium carbide deposits into the one plate.
Hyster wear plate is bolted or welded into equipment high wear areas to enhance wear resistance. Hyster can also custom fabricate Hyster wear plate to suit your requirements.
Micro-Structure: Mixture of hgh volume hexgonal shaped chromium carbide in tough austenitic &Martensitic
Penetration to the base metal:1.5mm
Cold forming: Minimum Radius:150mm (for 6+4) Suggested:using hydrolic press to bend plate
Cutting: Plasma (From backing plate side)/ Laser Cutting/ Water Jet Knife
I) Hardness: HRC> =58(HB> =600)
II) Chemistry: 3.5 to 6.5% C
15 to 35% Cr
1.0 to 2.5% Mn
0.7 to 2.0% Si
III) Microstructure: Refined austenitic chromium carbide alloy containing 30-50% carbides.
*We can accept OEM&ODM orders. Other thickness, please contact us for more information.
Standard Overlays | Weight sq/m(kg) | Standard Sheet Size(mm) | Overall Thickness |
4 ON 4 | 62 | 1500x3000 / 1200x2400 | 8 |
4 ON 6 | 77 | 1500x3000 / 1200x2400 | 10 |
6 ON 6 | 92 | 1500x3000 / 1200x2400 | 12 |
5 ON 8 | 100 | 1500x3000 / 1200x2400 | 13 |
6 ON 8 | 108 | 1500x3000 / 1200x2400 | 14 |
5 ON 10 | 116 | 1500x3000 / 1200x2400 | 15 |
9 ON 10 | 146 | 1500x3000 / 1200x2400 | 19 |
10 ON 10 | 157 | 1500x3000 / 1200x2400 | 20 |
12 ON 12 | 162 | 1500x3000 / 1200x2400 | 24 |
17 ON 12 | 222 | 1500x3000 / 1200x2400 | 29 |
Hyster White Iron Wear Block(700BHN-63HRC)-- Range of products based on a composite white iron wear surface metallurgically bonded to a weldable mild steel backing plate. Wear block is fixed to the surface of fixed and mobile plant equipment, such as mining buckets and chutes, where protection from severe abrasion is required.
Hyster Overlay Wear Plates--Chromium carbide clad wear plate manufactured in HYSTER and marketed worldwide. Overlay plate is well suited to fixed and mobile plant equipment associated with the construction, mining and resource industries; particularly iron ore, coal, cement and steel applications.
Hyster NiHard--Abrasion and high impact resistant product. It is often cast into billets and liners and used extensively in the mining, construction and mineral processes industries, particularly in bulk handling situations.
Hyster Tungsten Carbide-High standard abrasion resistant product. It is often used where the application has no impact force or very slightly impact.
Features and Benefits
Reduced Maintenance
• Protects any high wear area, eliminating the need for frequent rebuild or replacing wear plate
• Lasts longer than other wear protection
• Excellent alternative to hard facing which can lead to cracking of major structural components Increased Productivity
• Reduced maintenance ensures maximum machine availability
• Wide variety of shapes and sizes allows small areas to be protected, minimizing the affect on penetration and material flow
Lower Operating Cost
• Can be fit to flat or curved surfaces, eliminating the need to have wear plate formed to fit
• Bucket life is significantly increased, minimizing repair and new bucket orders
Typical Data Numbers:
>white iron wear blocks life is 50% greater than that of Ni Hard Irons.
>At least 7 times longer than A.R. type steels 360/400 BHN
>5 times the wear rate of Manganese Steel
>3 times the wear rate of Tapco Weld Hardfacing
>4 times the wear rate of Astralloy-Vulcan
>16 times the wear rate of Carbon Steel
>3 times the wear rate of 500 BHN A.R. Plate
Hyster offer our clients a wide range of wear products and professional wear solutions. We also welcome custom made one off's and consumables.
Following are our laminated wear blocks:
Types---the most common ones are:
1) Chocky bars (CB 25. CB40, CB50, CB65, CB80, CB90, CB100, CB130. CB150)
2) Standard wear bars (DLP201A, DLP 125, DLP184, DLP528, DLP619, DLP451, DLP450, DLP2230, DLP2017, DLP4, DLP919, DLP1191, DLP515, DLP200, DLP271, DLP270, DLP508, DLP115, DLP337, DLP1101, DLP343 )
3) Shaped wear bars
4) Wear buttons& donuts(WB60, WB75, WB90, WB110, WB115, WB150, DLP1920, DLP1921, DLP1994, DLP2196)
5) Shredder/Grinder hammer tips (DLP1654,90X90X50mm; DLP653,90X90X45mm; DLP1927, 90X90X55mm)
6) Bi-metallic wear plates
7) Knife edges(DLP1065-22, 203X22X50MM; DLP1265-22,305X22X50MM; DLP1065A-16, 203x16x50mm, DLP1065A-25, 203x25x62mm; DLP1265A-25, 305x25x56mm)
8) Skid bars, skid blocks(DLP412, 250x150x45mm; DLP413, 200x150x45mm; DLP414, 250x250x45mm)
9) Elbow wear blocks
10) Other sizes and shapes
11) Multi-function gradient cutter tooth
12) Rockbox liners
13) Micro-ledges