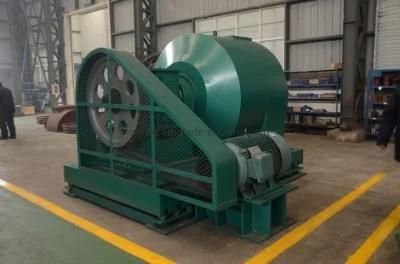
Dewatering Machine Centrifuges for Solid Liquid Separation
CITICIC Luoyang Heavy Machinery Co., Ltd.- Type:Flotation Separator
- Voltage:220V
- Weight:>10T
- Material:Casting Steel
- Certification:ISO9001:2008, CE
- Warranty:2 Years
Base Info
- Color:Customed Designed
- Customized:Customized
- Condition:New
- Transport Package:According to The Customer′s Requirement
- Trademark:cic
- Origin:China
Description
Part Name
Unit.
Numerical Value
1
Feed size
mm
0~25
2
The screen cloth works area
m2
1.88
3
Handling capacity per hour
t/h
140~200
4
The percentage of product water discharge
%
5~8
5
Strainer big end diameter
mm
1200
6
Strainer slit
mm
0.5
Main electrical machinery
Model
Y280S-4-V1
7
Power
kw
75
rotating Speed
r/min
1480
Lubricates the electrical machinery
Model
Y90L-4
8
Power
kw
1.5
rotating Speed
r/min
1400
9
External dimensions
Long × wide × high
mm
3160 × 2460 × 2680
10
Gross weight
kg
9121
Installation And Testing:
When the centrifuge is assembled completely in the manufactory, the test should be carried out in air operations. It should be sent out to the users in the form of machine after it is up to the requirements, the users can directly follow the steps to install the equipment when they get receipt of it.
1. Installation Step
1) Check whether the basis of surface is level, if it is uneven, adjust the leveling pad. Check the ground pin-hole size and pore size of the centre. Check whether the basis of elevation to meet the requirements.
2) Mount the shock absorber to the ground pin holes, install the nut first but not tightened until the machine is in the right place, then solid-tight.
3) Hoisting the machine in the place, tighten anchor bolts, tighten the upper pairs of nuts before the measurement with the caliper pad diameter, it is required that the diameter of compact size should be increased 2~3mm than the first fasten one.
2. Test Step
1) Checked before testing items
a. All bolts connections should be tighten
b. There is no equipments which have effects on the machine operation.
c. Make sure the pulley can be moved with both hands so that the machine can be rotated flexibly with non-stuck and abnormal noise.
d. Make the belt hang right.
e. Indicator within the oil tank should be located in the groove between the upper and lower limits.
2) Commissioning and inspection of the project
Meet the above requirements, follow these steps, and start running in the air for 8 hours.
a. Open the oil pump motor
b. Observe the oil supply situation, make sure everything is ok, open the console.
c. While there is no abnormal noise, stable operation, measure the amplitude of the centrifuges in the horizontal plane and make sure that it is less than 0.3mm.
d. Measure the oil temperature every 30 minutes, ensure the oil temperature rising is no more than environmental temperature-30ºC.
3) Loading Test
When all functioning of the machine working in the air is normal, then gradually feeding at the same time pay attention to the functioning of the device, while there is no abnormal phenomenon, the handling capacity can be increased to150~200t/h, the handling capacity of the material easily dehydrated can be larger, difficult to dehydration material handling capacity can be smaller. Add enough materials, it may take the measurement as the following items, when all meet the requirements, the equipment can be put into use.
a. Checked by commissioning and inspection items
b. Measuring capacity
c. Moisture measurement products
d. Measurement original compound, the content of grain size of less than 0.5mm
e. Measurement of centrifugal fluid solids
f. Measuring power consumption
Operation And Maintenance:
1. Operation
1) Pre-drive checks
a. Check the machine whether in full state and the connectors are loosening.
machine and the oil spill out of the pipeline.
c. Moving the pulley, check whether the machine is resisted and the belt tensioning situation.
d. Check whether the oil level inside the tank between the upper and lower limits of the oil indicator, enable the pipeline junction leakage are prohibited.
2) Driving
a. Activate the pump motor, to observe the oil flow table.after the oil flow through 1~2 minutes, then start the main motor.
b. When the machine is running in the normal condition, begin to feed, the charging capacity should be gradually increased.
3) Parking
a. Stop feeding, get the closure of the host after 2~3minutes.
b. Shut main motor down after half a minute, and then close the pump motor.
2. Maintenance
Centrifuge normal maintenance plays an important role in preventing accidents and injury in the weight of link components in the device's using, and the systems should be required to perform.
1) Lined lid is easy to wear and tear, open the lid or observe the lid abrasion situation from the observation hole, if the abrasion is serious, it should be replaced promptly.
2) Distribution cone is mounted on the top of the rotor body, contacted with material directly and easy to wear and tear. Every time when you change the screen and scraper, pay attention to check the distribution of the remaining tapered wall thickness, if it is too thin, take replacement timely.
3) Screen is the key part of the centrifuge, it is forbidden that there is no wire, wood, bolts and debris in the machine while it is used. For a long time using, if a little screen surface was damage, it allowed to be repaired by welding, but if the gap in the screen is as large as 0.75mm wear or screen seriously worn, the screen should be replaced. Likewise, if the mesh repair welding area is too large, re-do before the use of dynamic balance.
4) Spiral scraper, it should be paid attention to adjust the gap between blade and the screen surface when it is working, usually 0.3~1.5mm.If the gap is too large, it can mount the adjustment pads on the top of the rotor body underside for each additional pad, the gap decreased 0.34mm.If the adjustment of all cushion mount to the lower part, the gap remains large, replace the blade. It should pay attention to the pairs of containers while changing scraper, mount the weight of two scraper into a symmetrical position to keep the rotor body balancing performance. After replacement of the scraper, the machine should be conduct and test run in the air operation. If the rotor vibration is too large, it would have to do the rotor body balancing.
5)Export the protection lining, materials get through the lower scraper with the influence of centrifugal force, the material is left out in the protection of lining, and then fall until the belt exit cone machine, it should pay attention to the protection liner wear circumstances from the hole observed when it is used. When serious damage happened, replace it timely.
6) The export cone is at bottom of the machine, when material falls, the cone inner surface is often worn in use, and the lining should be checked regularly. If there is some damage, it must be promptly replaced.
7) The differential is a driving part of the machine, it should be aware of the lubrication conditions when it is used. It should pay attention to whether the oil is spilled, oil flow table is oil flow and the differential pulley-side and the upper part of bell-shaped cast-side sealing department have leaked oil. Enable that there is not any unusual noise in the working differential.
8) Lubrication system. It should be always checked the oil spill situation, pressure gauge and oil flow sheets. Oil filters in the filter and the oil tank strainer should be periodically cleaned or replaced. The oil level in the fuel tank must be within the upper and the lower limits shown in the table.
9) Cleaning the materials inside the machine regularly, rinsing the materials between the hood and lining surplus with red bell-shaped water, cleaning the appearance of the machines and the places around the equipment, make sure it is working in good condition.