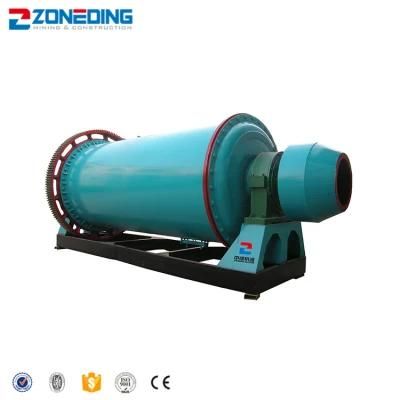
Cement Ceramic Dry Ore Mining Machine Wet Grinding Powde Gold Crusher Ball Mill Bearing
Zhengzhou Zhongding Heavy Duty Machine Manufacturing Co., Ltd.- Type:Ball Mill
- Motor Type:DC Motor
- Motor Power:15-1000kw
- Rotationl Speed:23-25r,min
- Application:Refractory Material, Silicate, Building Material
- Materials:Feldspare,Zinc Ore, Copper Ore, Gold Ore,Silica
Base Info
- Condition:New
- Warranty:One Year
- After-sales Service:One Year
- Flowchart:Provided
- Installation&Training:Provided
- Grinding Method:Wet or Dry
- Transport Package:by Sea
- Specification:customization
- Trademark:ZONGDING
- Origin:China
- Production Capacity:1-200t,H
Description
Specific operation
Installation and commissioning
Ball mill installation:
a) The installation plan is designed according to the user's basic project, and the installation should be carried out according to the direction, location and space shown in the figure;
b) The bottom plane of the fuselage should be firmly on the ground, and the level of the bottom plane of the cylinder after level adjustment should not be greater than 1.5/1000;
1. Installation
a) Remove the foreign matter in the reserved hole of the installation equipment foundation, especially the inner wall of the hole must not have dust, oil, water and other liquids;
b) After unpacking the packing box, use appropriate lifting equipment (crane/forklift) to move the host to the installation location;
c) Place the equipment in a good position, put the "living feet" that came with the machine on the anchor studs and weld them to the chassis of the frame in the anchor bolt installation holes, and then perform secondary grouting;
d) Tighten the nut and load the test machine after installing the cement up to the strength for 24 hours;
e) Connect to the power supply;
f) Installation inspection and correction of improper parts;
g) The electrical cabinet is placed in the auxiliary machine room, and no feet are required.
2. Trial operation:
After the ball mill is installed and passed the test, it can be run empty. The trial run of the ball mill should be carried out by a skilled ball mill operator and strictly abide by the safety operation rules of the ball mill.
(1) The continuous operation time of dry operation shall not be less than 12-24 hours, and problems found during operation shall be solved in time.
(2) The load test operation can be carried out when the dry run test machine is normal. The load test run should be carried out in stages. During load operation, the feed should be carried out according to the discharge situation to avoid unnecessary wear and damage of the steel balls and the cylinder liner. .
a) Add appropriate materials and 1/3 of the number of steel balls (refer to the general drawing of the ball mill for the maximum ball load) and run for 12-24 hours.
b) Add up to 2/3 of the number of steel balls to run for 24-48 hours.
c) According to the discharge situation of the ball mill, the output of qualified products, refer to the actual ball size of the ball mill of the same kind of concentrator, determine the reasonable ball size of the ball mill, and conduct a trial operation for not less than 72 hours.
(3) The increase of the above-mentioned load and the length of trial run time shall be determined based on the running-in conditions (temperature rise, noise, tooth surface contact, etc.) of the large and small gears and the gears of the reducer. Before the tooth surface contact accuracy does not meet the design requirements, it must not be operated at full load.
(4) The cooling and lubrication system should work normally during the trial operation, and the temperature of the main bearing, transmission bearing and reducer should be normal.
(5) After loading 2/3 of the number of steel balls and running for 24-48 hours, all bolts should be checked and tightened again.
(6) All records must be carefully made for trial operation.
The ball mill is mainly used for the mixing and grinding of ceramic raw materials. It is a necessary equipment for the production of various ceramic products. The machine adopts auto-coupling decompression to start to reduce the starting current. Its structure is divided into integral and independent types. It adopts V-belt drive, single-stage or double-stage deceleration, equipped with independent low-power motor for loading and unloading
The ball mill should be installed on a solid concrete foundation. For the basic design and construction of the ball mill, please refer to the ball mill assembly drawing and foundation drawing. In order to ensure that the position accuracy of each part of the ball mill does not change greatly during use, the foundation of the ball mill should adopt a monolithic structure.
After the compressive strength of the concrete foundation reaches 75% or more, the ball mill can be installed on it. Prior to installation, the quality of the foundation should be inspected. It is required that the concrete has no defects that affect the strength, the number and location of the reserved holes meet the requirements, and there is no debris, water, and oil in the reserved holes. When the "ground wire method" is used for installation operations, the "center target board" should be pre-embedded on the surface of the foundation. Before installation, draw all centerlines on the foundation and make eye-catching punch marks on the "center target board" as the centerline reference during installation.
Before hoisting, the ball mill should be fully inspected and accepted in different parts, and problems should be dealt with in time.
1. Refer to the assembly drawing of the main bearing components for the specific requirements of the main bearing part.
2. Refer to the assembly drawing of the rotating part for the cylinder part.
3. For the transmission part, please refer to the assembly drawing of the transmission part.
4. Refer to the assembly drawing for the overall relative position.
Working Principle
The ball mill is composed of a horizontal cylinder, a hollow shaft for feeding and discharging materials, and a grinding head. The cylinder is a long cylinder with a grinding body installed in the cylinder. The cylinder is made of steel plate. The steel liner is fixed to the cylinder. The grinding body Generally, it is a steel ball, which is packed into the cylinder according to different diameters and a certain proportion, and the grinding body can also be made of steel. Choose according to the particle size of the grinding material. The material is loaded into the cylinder by the hollow shaft at the feed end of the ball mill. When the cylinder of the ball mill rotates, the grinding body is attached to the cylinder liner due to inertia, centrifugal force and friction. Carried away by the cylinder, when it is brought to a certain height, it is thrown down due to its own gravity. The falling grinding body crushes the material in the cylinder like a projectile.
The material enters the first chamber of the mill uniformly through the feeding device through the hollow shaft. The chamber has a step liner or a corrugated liner, which contains various specifications of steel balls. The rotation of the cylinder generates centrifugal force to bring the steel balls to a certain level. Falling after the height, it will have a heavy blow and grinding effect on the material. After the material reaches the rough grinding in the first bin, it enters the second bin through the single-layer partition board. The bin is lined with a flat liner and steel balls inside to further grind the material. The powder is discharged through the discharge grate plate to complete the grinding operation.
When the barrel is rotating, the grinding body also slips off. During the sliding process, the material is ground. In order to effectively use the grinding effect, when grinding the material with larger particle size, the grinding body is fine. Divided into two sections by a partition board, it becomes a double silo. When the material enters the first silo, it is crushed by the steel ball. When the material enters the second silo, the steel section grinds the material, and the ground qualified material is hollow from the discharge end. When the shaft is discharged to grind materials with small feed particles, such as sand No. 2 slag, coarse fly ash, the barrel of the mill can be formed as a single-chamber barrel mill, and the grinding body can also be made of steel.
The raw materials are fed into a hollow cylinder through a hollow shaft journal for grinding, and the cylinder is equipped with various diameters of grinding media (steel balls, steel rods or gravel, etc.). When the cylinder rotates around the horizontal axis at a certain speed, the medium and raw materials contained in the cylinder will be separated from the cylinder as the cylinder reaches a certain height under the action of centrifugal force and frictional force. The inner wall is projected to fall or roll down, crushing the ore due to the impact force. At the same time, during the rotation of the mill, the sliding movement between the grinding media also has a grinding effect on the raw materials. The ground material is discharged through the hollow journal.
Technical Parameters
Note: Any change of technical data shall not be advised additionally.
Application:
Structural features
(1) The main bearing adopts a large-diameter double-row spherical roller bearing instead of the original sliding bearing, which reduces friction and energy consumption, and the mill is easy to start.
(2) The end cap structure of ordinary mills is retained, with large diameter inlet and outlet ports, and large processing capacity.
(3) The feeder is divided into two types: combined feeder and drum feeder, with simple structure and separate installation.
(4) There is no inertial impact, the equipment runs smoothly, and the maintenance time of the mill is reduced and the efficiency is improved.
Ceramic liner can avoid iron pollution and other impurity.
Customer Case
Mongolia Limestone Grinding Project
Input Size: 20mmOutput Size: 150meshCapacity: 50t/h
Equipment: Φ2100X2400 Ball Mill, Dust Collector, Ball Mill Spare Parts